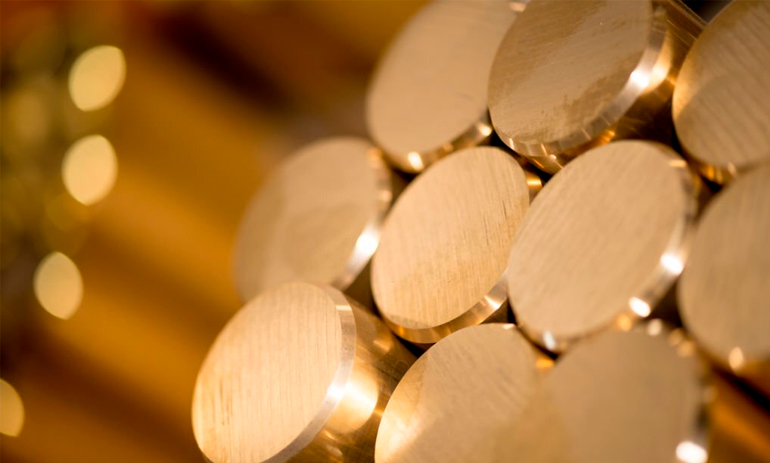
C27450
UNS C27450, often referred to as yellow brass, is characterized by a copper content of no less than 62%. In the realm of cold forming processes, CuZn37 stands as the predominant brass alloy. Despite the fact that brasses with lower zinc content exhibit superior cold forming properties, CuZn37 remains the most widely utilized alloy. This preference can be attributed to a combination of factors. Firstly, it is economically advantageous due to the lower cost of zinc when compared to copper. Additionally, the forming characteristics of this alloy align well with the requirements of a wide range of applications, making it a versatile and practical choice.
CHEMICAL COMPOSITION
Elements | Min (%) | Max (%) |
Cu | 60.00 | 65.00 |
Pb | – | 0.25 |
Fe | – | 0.35 |
Total Others | – | 0.50 |
Zn | Remainder |
MECHANICAL PROPERTIES ACCORDING TO ASTM B927 (AS PER TEMPER HO2)
Range (Inch) | From | To | UTS Min (Ksi) | PS Min (Ksi) | Elongation Min (%) | Hardness Min | Hardness Max |
Round (Dia) | 0.059 | 0.500 | 53 | 33 | 10 | – | – |
0.500 | 1.000 | 48 | 30 | 13 | – | – | |
1.000 | 2.953 | 43 | 28 | 15 | – | – | |
Hexagon (A/F) | 0.118 | 0.500 | 53 | 33 | 10 | – | – |
0.500 | 1.000 | 48 | 30 | 13 | – | – | |
1.000 | 2.756 | 43 | 28 | 15 | – | – | |
Square (A/F) | 0.118 | 0.500 | 53 | 33 | 10 | – | – |
0.500 | 1.000 | 48 | 30 | 13 | – | – | |
1.000 | 2.362 | 43 | 28 | 15 | – | – | |
Rectangle (Thickness) | 0.118 | 0.500 | 53 | 33 | 10 | – | – |
0.500 | 1.000 | 48 | 30 | 13 | – | – | |
1.000 | 1.969 | 43 | 28 | 15 | – | – |
Range (mm) | From | To | UTS Min (MPa) | PS Min (MPa) | Elongation Min (%) | Hardness Min | Hardness Max |
Round (Dia) | 1.5 | 12 | 365 | 230 | 10 | – | – |
12 | 25 | 330 | 205 | 13 | – | – | |
25 | 75 | 295 | 195 | 15 | – | – | |
Hex (A/F) | 3 | 12 | 365 | 230 | 10 | – | – |
12 | 25 | 330 | 205 | 13 | – | – | |
25 | 70 | 295 | 195 | 15 | – | – | |
Square (A/F) | 3 | 12 | 345 | 170 | 10 | – | – |
12 | 25 | 310 | 115 | 20 | – | – | |
25 | 50 | 275 | 105 | 20 | – | – | |
Rectangle (Thickness) | 3 | 12 | 345 | 170 | 10 | – | – |
12 | 25 | 310 | 115 | 20 | – | – | |
25 | 50 | 275 | 105 | 20 | – | – |
PHYSICAL PROPERTIES | |
Melting Point – Liquidus°F | 1680 |
Density lb/cu in. at 68°F | 0.31 |
Specific Gravity | 8.44 |
Electrical Conductivity % IACS at 68°F | 27 |
Thermal Conductivity Btu/ sq ft/ ft hr/ °F at 68°F | 67 |
Coefficient of Thermal Expansion 68-57210⁻⁶ per °F (68 – 572°F) | 11.4 |
Specific Heat Capacity Btu/ lb /°F at 68°F | 0.09 |
Modulus of Elasticity in Tension ksi | 15000 |
Modulus of Rigidity ksi | 5600 |
FABRICATION PROPERTIES | |
Technique | Suitability |
Soldering | Excellent |
Brazing | Excellent |
Oxyacetylene Welding | Good |
Gas Shielded Arc Welding | Fair |
Coated Metal Arc Welding | Not Recommended |
Spot Weld | Good |
Seam Weld | Not Recommended |
Butt Weld | Good |
Capacity for Being Cold Worked | Excellent |
Capacity for Being Hot Formed | Fair |
Machinability Rating | 35 |